球化剂在铸造行业应用的四大痛点及工业解决方案
在铸铁向球墨铸铁蜕变的核心工艺中,球化剂如同金属基因的编辑师,其控制精度直接决定铸件性能。然而,铸造现场常因反应失控、效果衰减、组织异常等问题导致巨额损失。本文将深度解析球化剂应用的四大技术痛点及系统性解决方案,为行业提供可落地的技术路径。

痛点一:剧烈反应与镁吸收率低下——生产安全与成本的博弈
问题本质
高镁球化剂(Mg 7-8%)遇1480℃以上铁水时,镁元素汽化率超70%,引发喷溅、浓烟及安全事故,同时造成镁吸收率仅30%-40% 的资源浪费。
关键技术对策
1. 温控缓释工艺
铁水处理温度严控1420-1480℃,选用钙含量>2%的球化剂。钙形成熔渣保护膜,抑制镁蒸气逃逸,反应平稳度提升50%以上。
2. 盖包法革命性升级
密封处理包使镁吸收率突破60%,烟尘捕获率达90%,车间污染指数下降75%。实证显示球化剂用量减少15%,年成本节省超百万。
3. 流体动力学包型设计
浇包高径比从1:1调整为2:1,延长镁蒸气在铁液中的溶解路径,逃逸率降低40%。
痛点二:球化衰退倒计时——浇注延误引发的性能崩塌
失效机制
处理后的铁水中,镁元素以每分钟0.001%的速度与硫/氧反应消耗。浇注延误超8分钟,石墨球化率可从85%暴跌至50%,导致某汽车厂转向节批量脆断事故。
衰退阻断方案
1. 稀土元素战术增援
钇(Y)基重稀土球化剂抢占硫/氧结合位点,为镁构建防护盾,有效时间从8分钟延至15分钟,风电轮毂低温冲击韧性达标率提升至98%。

2. 硫氧预净化双阶控制
高硫铁液(S>0.05%)采用氧化镁脱硫剂预处理,脱硫率85%以上,将硫压至0.015%安全阈值,减少镁消耗源。
3. 瞬时孕育接力技术
浇注前注入含锶硅铁孕育剂,0.5秒内激发石墨形核,抵消衰退影响,薄壁件球化合格率提高30%。
痛点三:白口化脆变——过量添加的隐性代价
缺陷成因
球化剂过量或稀土残留>1%时,铸件边缘形成碳化物硬质层(硬度>500HB),韧性趋近于零。某农机齿轮箱因0.3mm白口层导致装配崩裂,单次损失达50万元。
精准平衡策略
1. 低稀土配方适配
中小铸件选用稀土≤1%的镁球化剂(如3-8型),碳化物生成指数下降60%。
2. 热分析动态调控系统
浇包内置热电偶,实时解析冷却曲线调整孕育剂量,10秒内完成白口风险干预,废品率降低至1.5%。
3. 薄壁件随流孕育补偿
0.5mm以下壁厚区域采用硅钡钙随流注入,石墨形核密度增加120%,消除边缘脆化。
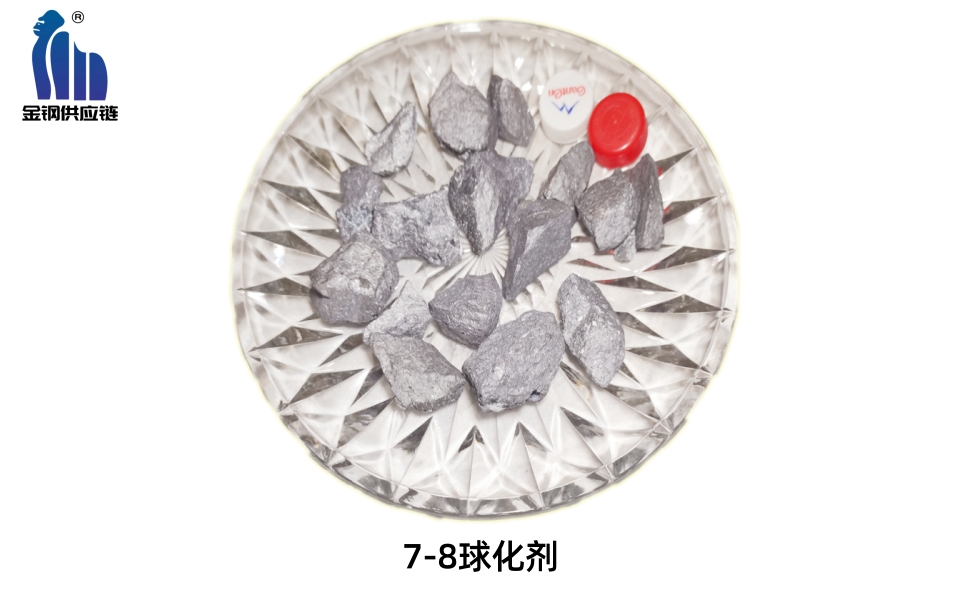
痛点四:硫元素的致命干扰——纯净度缺失的连锁反应
破坏性机理
硫(S)含量>0.025%时,与镁结合生成MgS渣相,导致球化不良率激增。某管道厂因硫偏析引发局部爆裂,压力测试损失超千万元。
硫干扰根治路径
1. 氧化镁深度脱硫
熔炼后期加入MgO基脱硫剂,硫残留≤0.008%,渣量比氧化钙工艺少30%,适配连续生产线。
2. 高抗硫球化剂定制
针对刹车盘等回炉料(S>0.04%),采用铈镧稀土球化剂,优先形成Ce₂S₃高熔点化合物,保障有效镁含量。
3. 喂线技术精准投送
合金包芯线直插铁液深处,成分控制精度±0.005%,抗硫干扰合格率提升至99.2%。

技术前沿:绿色化与智能化的双重进化
行业正经历三大变革:
1. 环保型配方革新
低镁高钙球化剂(Mg≤5%)减少烟尘30%,稀土减量化降低战略资源依赖。
2. 数字孪生过程控制
物联网系统实时分析铁水成分,自动计算最佳加入量,误差率<2%,废品率再降40%。
3. 微观组织AI预测
深度算法通过冷却曲线预判石墨形态,球化合格率预判准确度达95%。
从蒸汽阀门到风电巨轮轴承座,球墨铸铁的每一次性能突破,都是对球化剂应用痛点的战略级攻克。当稳定性、时效性、纯净度、组织控制四大核心命题被逐一破解,铸造行业正从经验驱动迈向数据驱动的精密时代——这不仅是技术的胜利,更是对金属本质深刻理解的智慧结晶。