95%石墨化增碳剂冶金应用实战指南:5大常见问题与解决方案
在冶金行业,95%石墨化增碳剂因高碳含量(≥95%)、低硫(≤0.5%)、低杂质特性,被广泛用于提升钢材性能和降低成本。但在实际应用中,操作不当或选型错误可能导致吸收率低、铸件缺陷等问题。金钢供应链结合行业实战经验,解析高频问题并提供解决方案,助您高效避坑。

一、关键问题1:吸收率不稳定(60%-90%波动)
典型表现:
增碳剂漂浮在铁水表面,难以溶解;
碳含量实测值低于理论值,吨钢成本增加10%-15%。
原因与解决方案:
1. 投料时机错误
错误操作:铁水熔炼后期加入,温度过低(<1450℃)导致增碳剂无法充分扩散。
正确操作:随废钢等炉料同步投入,利用高温熔炼阶段(>1500℃)促进溶解。
2. 粒度不匹配
错误案例:10吨电炉使用1-3mm细粉,增碳剂被气流吹散。
匹配建议:
≤1吨炉:0.2-1mm细粉(比表面积大,溶解快);
1-10吨炉:1-5mm颗粒(平衡下沉速度与溶解效率)。
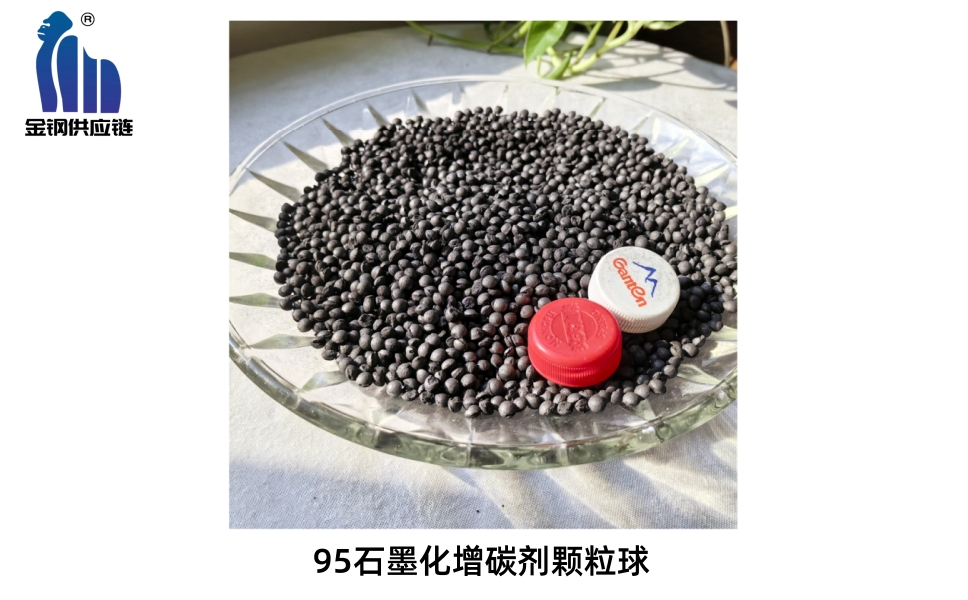
二、关键问题2:硫、氮杂质引发质量缺陷
危害表现:
硫含量>0.1% → 铸件产生气孔、热裂;
氮含量>500ppm → 厚壁铸件出现裂隙状氮气孔。
选型与工艺优化:
1. 源头严控杂质
选用高温石墨化石油焦增碳剂(2800℃处理),硫≤0.03%、氮≤200ppm。
2. 复合脱硫工艺
增碳剂+0.2% CaC₂(电石)协同脱硫,硫残留量降至0.02%以下。
三、关键问题3:增碳不均导致成分偏析
典型场景:
大型铸件芯部碳含量比表面低0.3%-0.5%,引发硬度不均。
解决策略:
1. 机械辅助扩散
投入增碳剂后,用惰性气体(氩气)底吹3-5分钟,均匀性提升40%。
2. 分层添加法
分3次加入增碳剂(炉底30%、中期40%、出铁前30%),避免集中堆积。
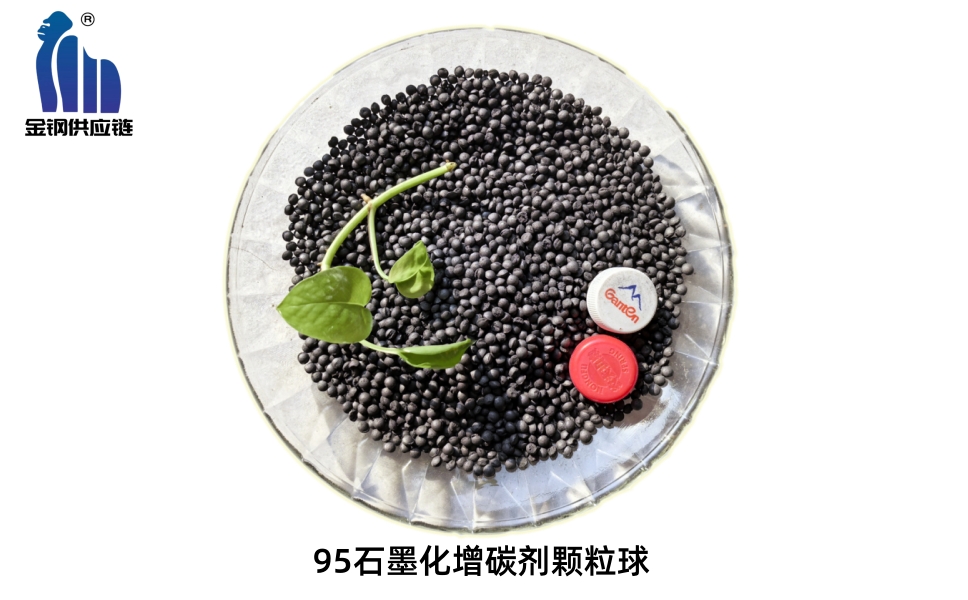
四、关键问题4:误用非石墨化增碳剂的隐性风险
劣质品危害对比:

避坑要点:
索要石墨化工艺证明(2800℃以上高温处理);
检测微观结构:真石墨化增碳剂在显微镜下呈片层状石墨结晶。
五、关键问题5:环保与成本平衡难题
行业痛点:
石墨化工艺能耗高,部分企业为降本选用非石墨化产品,导致环保不达标。
创新解决方案:
1. 绿电配套
如宁夏某厂将矿热炉接入风电,吨增碳剂碳排放降低40%。
2. 废钢+增碳剂替代生铁
每增加10%废钢用量,搭配1.2%-1.5%石墨化增碳剂,吨成本下降200元。

实战选购与使用清单
1. 采购检验三步法:
Step1 查资质:生产许可证、第三方碳硫检测报告(GB/T 3795-2014);
Step2 测样品:送检碳含量、硫、氮、粒度分布;
Step3 看案例:考察合作钢厂应用数据(如某车企铸件良品率从88%→95%)。
2. 操作黄金守则:
温度>1500℃时投入,避免接触炉壁;
添加量=目标碳量×1.1(预留10%烧损)。
案例警示:2024年河北某铸造厂因使用硫超标的非石墨化增碳剂(0.45% S),导致200吨刹车盘批量气孔报废,直接损失160万元。
结语:科学应用是降本增效的核心
95%石墨化增碳剂绝非“一加了之”,需结合工艺适配性、杂质控制和精准投放。选择高纯石油焦原料+高温石墨化工艺的产品,并落实分层添加、气体搅拌等操作,方能实现吨钢降本200元+缺陷率下降30%的双重收益。